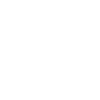
ZAPP Z M4 PM
Z-M4 PM is a tungsten molybdenum-vanadium high speed steel produced by powder metallurgy methods. It offers an excellent combination of wear resistance, red hardness, and toughness properties which can provide superior tool performance in a broad range of cutting tool and cold work tooling applications.
Chemical Composition
NO | DIN | C | Cr | Mo | V | W |
---|---|---|---|---|---|---|
Z M4 PM | Special Alloy | 1,42 | 4,00 | 5,25 | 4,00 | 5,50 |
Applications
- Cutting tools
- Punches and dies
- Fine blanking tools
- Shears, rotary shears
- PM compacting tools
- Cold extrusion dies
- Broaches
- Reamers
- Milling tools
Heat Treatment
HEAT TREATMENT | TEMPERATURE |
---|---|
Soft Annealing | Heat uniformly in a protective atmosphere (or vacuum) to 1600°F (870°C) and soak for 2 hours. Slow cool 30°F (15°C) per hour until 1000°F (540°C). |
Stress Relieving | Heat uniformly to 1100 – 1300 °F (595 – 700°C), soak for 2 hours, and cool in air or furnace. |
Hardening | Vacuum, salt, or protective atmosphere methods are generally used. Care must be taken to prevent decarburization. |
Tempering | Temperatures in the range of 1000°F (540°C) to 1100°F (595°C) are generally used depending on the hardness required. |
Relative Toughness
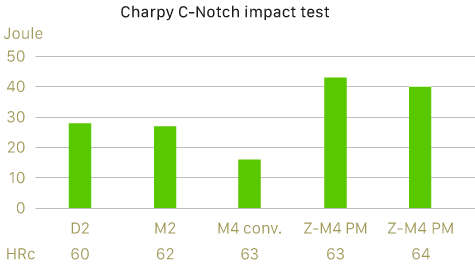
Relative Wear Resistance
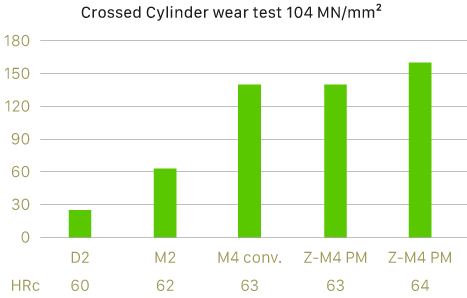
Delivery Conditions
225-255 HB
Temperlng Graph
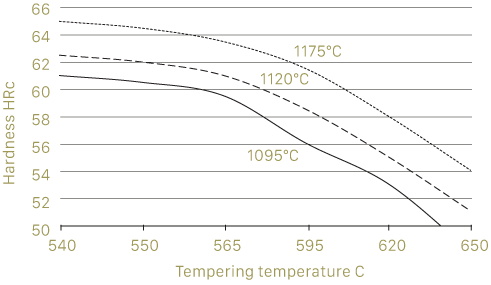
Required hardness HRC | Austenitizing soak temp. °C | Austenitizing soak time (min) | Tempering temperature °C |
---|---|---|---|
58-60 | 1095 | 25 | 550 |
60-62 | 1120 | 20 | 550 |
62-64 | 1150 | 15 | 550 |
63-65 | 1175 | 10 | 550 |
64-66 | 1190 | 5 | 550 |