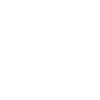
Astro® ESR
ESR (Electro Slag Remelting) hot work tool steel with very good toughness and cleanliness.
Chemical Composition
NO | DIN | C | Si | Cr | Mo | V | Mn | P | S |
---|---|---|---|---|---|---|---|---|---|
1.2343 ESR | X37CrMoV5-1 | 0,33-0,41 | 0,80-1,20 | 4,80-5,50 | 1,10-1,50 | 0,30-0,50 | 0,25-0,50 | Max 0,01 | Max 0,003 |
Material Properties
- High toughness and ductility.
- Very good microstructural cleanliness and homogeneity.
- Very good Polishability.
- Good hot strength and tempering back resistance.
- Very good texturing ability.
- Good weldability.
- Good machinability.
- Up to 54 HRc after heat treatment.
- Recommended working hardness 44-52 HRc.
- Good nitriding and coating ability.
Applications
- Precision Plastic injections molds,
- High gloss plastic injection moulds,
- Molds for piano black surfaces such as headlights lens molds.
- Molds for abrasive polymers and reinforced resins.
- Die casting dies for medium run
- Die casting dies of lighting and other large parts.
- Secondary sections on high pressure die casting dies for long run.
- Dies for all press forging applications.
- Cutting and shearing blades thicker than 10 mm.
- Cold forging and cold extrusion dies.
- Industrial knives resistant to ductile fracturing and breaking risks.
Heat Treatment
HEAT TREATMENT | TEMPERATURE |
---|---|
Soft Annealing | 750-800°C |
Stress Relieving | 600-650°C |
Hardening | 1020-1060°C |
Tempering | 530-700°C |
Physical Properties
20°C | 100°C | 400°C | 500°C | 600°C | |
---|---|---|---|---|---|
Elastic Modulus [kN/mm²] | 210 | - | 183 | 176 | 168 |
Thermal Expansion Coefficient [10ˉ6/K] | - | 10,7 | 11,8 | 11,9 | 12,4 |
Thermal Conductivity [W/mK] | - | 28,4 | 27,1 | 29,9 | 28,5 |
Delivery Condition
230 HB, Soft annealed.
Tempering Graph
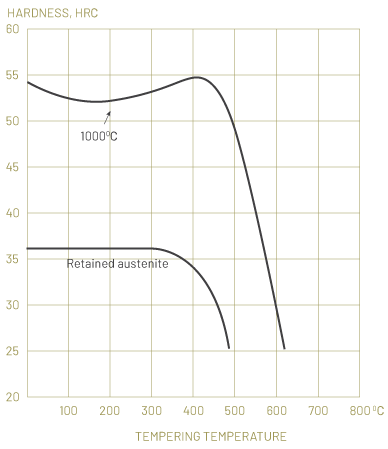